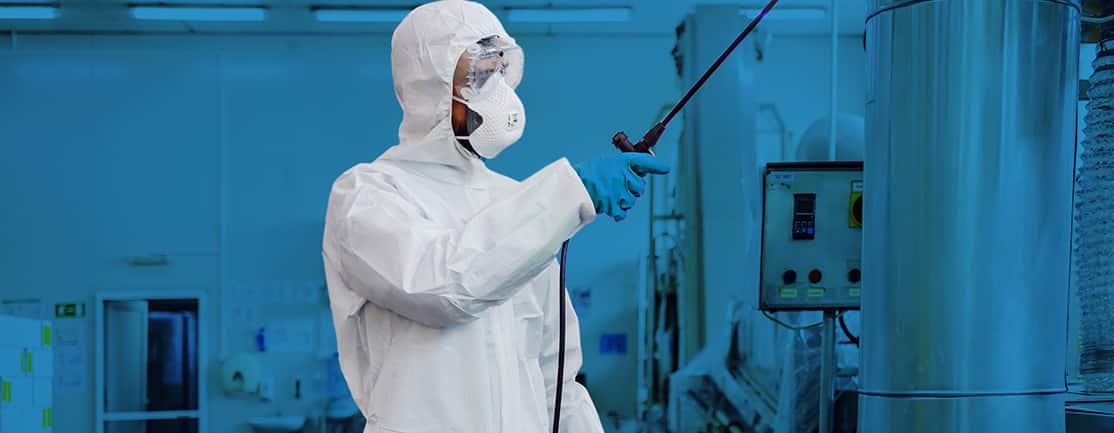
Supply chain visibility is critical to understanding the impact disruption has on every link in the chain and it allows others in the ecosystem to plan and take appropriate action. Disruptive events – such as the coronavirus pandemic – can only be navigated with robust and resilient systems in place. These systems require ‘circuit-breakers, fail-safe protocols and backups’ so that they can perform strongly during both business-as-usual periods and continue to create value despite disruption.
In our recent TRACC Community webinar How supply chain leaders are navigating COVID-19, Philipp Meier, European Supply Chain Lead, CCi, facilitated a discussion with three prominent CCi clients during which they shared the best practices and key learnings that are helping their organizations navigate the new normal. They also highlighted how continuous improvement programs can build resilience during times of uncertainty.
According to David Light, Operations Director at wet wipes manufacturer Nice-Pak International, the organization has seen a substantial increase in demand for antibacterial hand wipes during the pandemic period with a growth of over 300%. This resulted in a significant knock-on demand for some raw materials such as alcohol and non-woven fabric. “Fortunately, we’ve had long-standing relationships with a small group of suppliers which meant we could maintain a relatively stable product supply,” said David. “Simultaneously, there was a significant drop in demand on the cosmetics side, and we had to convert some lines to accommodate this volatility.
“Going into the pandemic crisis, many of our customers were looking at recyclable products. As a result, we were driving a substantial development program which, unfortunately, had to come to a temporary halt. The vast majority of customers were accepting of the decision and still wanted their products.”
Nice-Pak’s approach to the COVID-19 crisis involved five steps:
- Staying in line with Government advice and direction
- Activating a job retention scheme to accommodate a small group of people with specific health issues
- Changing terms and conditions of employment where the sick leave system offered a few days’ delay to prepare for self-isolation
- Ramping up communications with weekly updates and reminders of systems and processes
- Utilizing IT by speeding up the transition to cloud computing
“Since we are still in the early days of our TRACC implementation, we had to make sure that we keep our operations excellence program alive,” said David. “We decided to focus more on the education of our CI leads and process confirmation through Short Interval Control (SIC). We reduced the number of people attending the daily operations review and made the meetings much more focused and action-orientated. CCi is also supporting our change program with remote learning for QA technicians as well as establishing the Site Steering Committee (SSC) with remote support.”
Another business that experienced a sharp spike in demand amidst government lockdowns is Nomad Foods, a leading European frozen food company. John Orr, Head of Manufacturing Development said that organic revenue growth was 20% ahead of plan at the beginning of March when the pandemic struck. “After an initial period of pantry loading, growth is now being driven by in-home consumption and stock replenishment,” explained John. “All 13 of our factories remained open, and we acted early and decisively to implement new COVID-19 policies and procedures.
“Some of these procedures include the establishment of global and local Incident Management teams, daily senior leadership calls during peak hours, at-home working, and a strong recovery plan for return to work. Our SKU prioritization during peak periods has now shifted to SKU optimization during recovery, while our procurement teams are leveraging current market conditions to secure 2020 materials at an attractive price.
“We’ve also installed thermographic cameras at the entrances of each of our factories, secured an adequate supply of PPE, and placed social distancing and physical barriers. Like Nice-Pak, we implemented a reliable and consistent communications program, including employee rewards.”
Regular communication proved to be the key to building resilience and ensured continued traction of the Nomad OpX Program. “With the challenge of a no-travel policy, we have fully utilized our Webex platform to support the teams through weekly calls and remote training, driving a ‘One Team’ mentality,” said John. “In terms of community support, Nomad Foods established a €3.2 million fund to provide monetary and food donations to local humanitarian and healthcare organizations.”
Echoing his peers’ sentiments, Leo Zhang, CI Lead at global conglomerate Cargill, confirmed that communication is of the utmost importance. Said Leo: “During this unprecedented time, we work around the clock with farmers and our customers – the world’s food retailers and service providers – to maintain a safe, responsible, and sustainable supply of food.
“Our COVID-19 response initiatives included establishing a COVID Response Committee and setting up health emergency planning and response workflow. Our top priority remains the health and well-being of our employees as they are essential for delivering the food we need to stay healthy and nourished. To ensure their protection, we standardized work on environmental disinfection and supplied PPE.
“Many businesses are working faster and better than before, including us. To sustain this momentum, our focus will be on the Leading and Managing Change and Focused Improvement components of TRACC post-COVID-19. We want to maintain the current agile operating model by giving remote teams more decision-making authority and allowing cross-functional teams to solve problems via videoconferencing.
“Cargill is also in the process of digitalizing its entire value chain to become even more agile and responsive. For instance, we use advanced analytics to combine new sources of data, create a digital production system and workflow, and an online dashboard.”
For more supply chain resiliency insights, watch the webinar on demand here.